Well, here is some more inspiration for you
blacksmiths out there - and another history lesson
as well.
These are some of the flint strikers I made up
yesterday. And the historical time periods vary
quite a bit.
Left side from bottom:
- Found at the Fox Hill Seneca Indian village site up in New York.
- Found at the Cherry Hill Seneca Indian village site up in New York.
These two Indian village sites were in use from
1650 to 1680. The strikers are believed to be of
Dutch origin - from traders operating out of New
Amsterdam on Manhattan Island - before the British
captured it and renamed it New York.
- A Scottish flint striker. The British museum
dates this to the 18th century, and said it was
more decorative than the local British flint
strikers, and probably from the Scottish dealings
with France and Flanders were it was common. Note
the similarities with that Dutch striker from the
Cherry Hill village site. More than just coincidence.
- The top two on the left are Roman 1st to 3rd
century style flint strikers. There is a French
striker dated 1566 that has some similarities to
the top one, but otherwise these styles went out of
fashion several centuries before.
Right side from bottom:
- a Burgundian flint striker. The shape shows up
in the mid 1400's, and continued to be seen up into
the mid 1700's. It even shows up in several family Coat-of-Arms.
- an Irish flint striker. The British museum dates
it to the 18th century. Don't you just love those
museum 100 year date ranges. Note the similarites to
that Burgundian striker.
- Classic C striker. With that extra little curl
on only one end, this became pretty common in the
early 1800's, and is more generally associated with
the Western fur trade - Rocky Mountains.
- Classic Spanish Colonial or Mexican U shaped
flint striker. Usually called an Eslabone - which
means Link - because it resembles a chain link.
There are lots of little variations on these -
longer, shorter, thicker, with almost no gap in the
middle, with a gap wide enough to put your fingers
in it, almost V shaped, and with those extra little
curls bent/curled from either side of the bar.
There is also an Italian version dated 1634 where
the two little curls are bent/curled into the center gap.
The unique thing about those Scottish and Irish
flint strikers is that the British museum actually
identified them as Scottish and Irish. They
usually just give them that generic "British" or
"English" designations.
Just some more iron work to get people inspired to
beat up steel. And to show people some more
shapes/styles of flint strikers.
Now I have to work on some more of those "bar"
styles. Lots of variations with them - some being
some of the very first ever traded to the Indians
in North America. Yes, that very thin/small
"handle" was often broken off.
Have fun blacksmithing.
Mikey - that grumpy ol' German blacksmith out in the Hinterlands
blacksmiths out there - and another history lesson
as well.
These are some of the flint strikers I made up
yesterday. And the historical time periods vary
quite a bit.
Left side from bottom:
- Found at the Fox Hill Seneca Indian village site up in New York.
- Found at the Cherry Hill Seneca Indian village site up in New York.
These two Indian village sites were in use from
1650 to 1680. The strikers are believed to be of
Dutch origin - from traders operating out of New
Amsterdam on Manhattan Island - before the British
captured it and renamed it New York.
- A Scottish flint striker. The British museum
dates this to the 18th century, and said it was
more decorative than the local British flint
strikers, and probably from the Scottish dealings
with France and Flanders were it was common. Note
the similarities with that Dutch striker from the
Cherry Hill village site. More than just coincidence.
- The top two on the left are Roman 1st to 3rd
century style flint strikers. There is a French
striker dated 1566 that has some similarities to
the top one, but otherwise these styles went out of
fashion several centuries before.
Right side from bottom:
- a Burgundian flint striker. The shape shows up
in the mid 1400's, and continued to be seen up into
the mid 1700's. It even shows up in several family Coat-of-Arms.
- an Irish flint striker. The British museum dates
it to the 18th century. Don't you just love those
museum 100 year date ranges. Note the similarites to
that Burgundian striker.
- Classic C striker. With that extra little curl
on only one end, this became pretty common in the
early 1800's, and is more generally associated with
the Western fur trade - Rocky Mountains.
- Classic Spanish Colonial or Mexican U shaped
flint striker. Usually called an Eslabone - which
means Link - because it resembles a chain link.
There are lots of little variations on these -
longer, shorter, thicker, with almost no gap in the
middle, with a gap wide enough to put your fingers
in it, almost V shaped, and with those extra little
curls bent/curled from either side of the bar.
There is also an Italian version dated 1634 where
the two little curls are bent/curled into the center gap.
The unique thing about those Scottish and Irish
flint strikers is that the British museum actually
identified them as Scottish and Irish. They
usually just give them that generic "British" or
"English" designations.
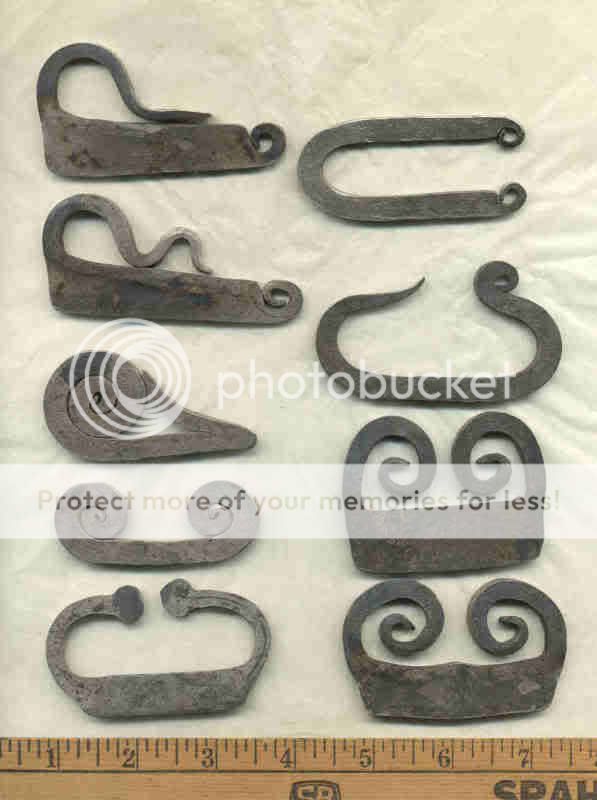
Just some more iron work to get people inspired to
beat up steel. And to show people some more
shapes/styles of flint strikers.
Now I have to work on some more of those "bar"
styles. Lots of variations with them - some being
some of the very first ever traded to the Indians
in North America. Yes, that very thin/small
"handle" was often broken off.
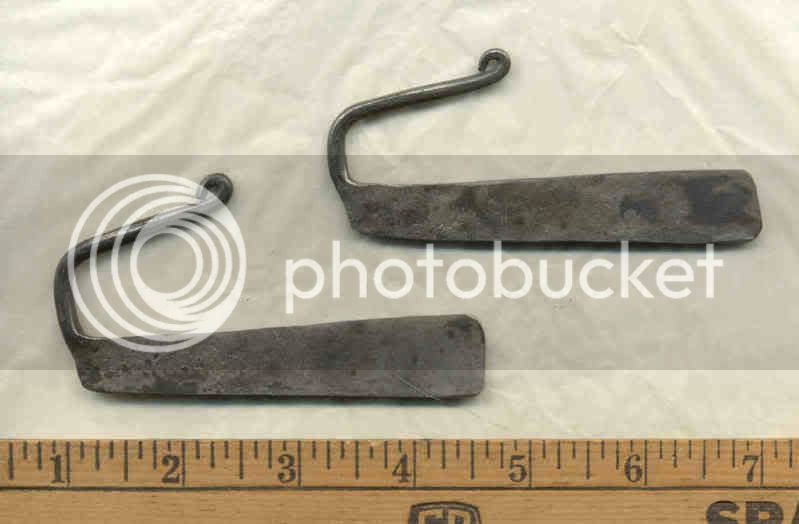
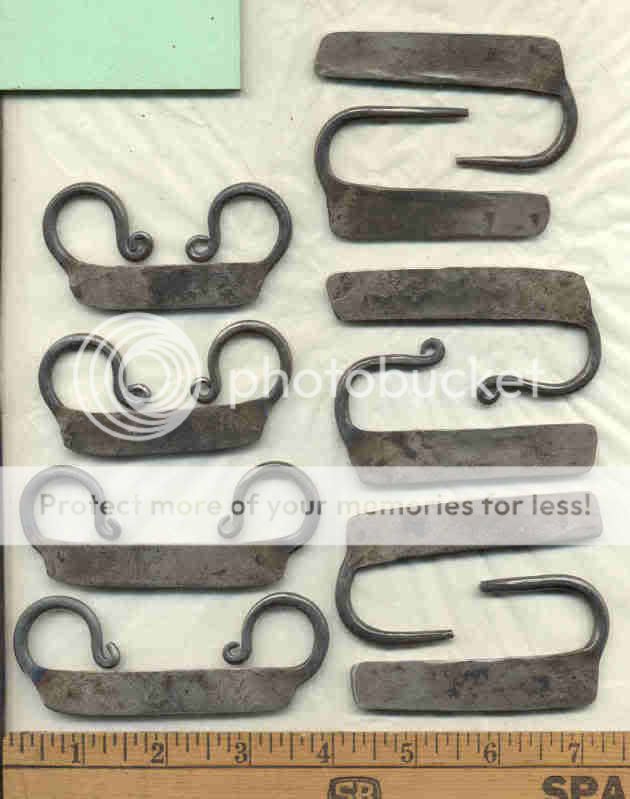
Have fun blacksmithing.
Mikey - that grumpy ol' German blacksmith out in the Hinterlands