I don't consider myself a master ball molder, but have several Lyman Steel molds and have had good success with them. I suppose I've run a few thousand ball through those molds.
Recently, I bought a Lee Aluminum mold in .575 for my recently built .58 Flint Hawken. I have to admit to having a heck of a time trying to get good ball with this mold. First, the lead kept bridging across the opening to the cavity. I finally ran the lead very hot...1000 degrees. This stopped the bridging and I was able to get several hundred ball done.
From a size and weight perspective they were pretty good. They measured .5745 + or - .0005. All but 23 of them weighed between 282 and 285 grs with the vast majority being 284 + or - 0.5 grs. I'm happy with these results.
HOWEVER, a good portion of the ball had defects around the sprue. Pictured below are two examples of the defect...also pictured are two good ones.
Since the weights and measurements were pretty good, I decided to do a 5-shot group with both types to see what happened. Pictures below are the results. Net, at 75 metres with the "good" balls a 2.25" group (measured center-to-center across the balls furthest apart. The "bad" balls had a 5.50 inch group. I swabbed the same between shots. There were no material delays in ignition or anything that would have caused me to flinch on any of these, so I think they are legitimate groups. Bench rested.
I really didn't think that this defect at the sprue would have this big of an impact, but clearly these ball need to go right back into the pot.
For those of you using Lee molds, have you experienced anything like this...the bridging issue, problems getting the cavity to fill properly unless you're running the lead very hot, etc.? I tried to keep the mold hot by holding it right on top of the pot while dipping, but clearly I was doing something wrong with this mold that I've not had any issue with while using my Lyman steel molds.
I also have to go back to some load development as the ToTW hand cast ball I used to work up my load turned out to be oversized by several thousandths...some even being bore sized! No wonder I was cutting patches, nearly bruising my hand on the short-starter, etc. Some poor quality control there. I'm going to bump my patch thickness a bit to "re-tighten" the load a bit and see if I can't get the "good ball" group shrunk down a bit. Need to tap that front sight over a bit too! :grin:
Recently, I bought a Lee Aluminum mold in .575 for my recently built .58 Flint Hawken. I have to admit to having a heck of a time trying to get good ball with this mold. First, the lead kept bridging across the opening to the cavity. I finally ran the lead very hot...1000 degrees. This stopped the bridging and I was able to get several hundred ball done.
From a size and weight perspective they were pretty good. They measured .5745 + or - .0005. All but 23 of them weighed between 282 and 285 grs with the vast majority being 284 + or - 0.5 grs. I'm happy with these results.
HOWEVER, a good portion of the ball had defects around the sprue. Pictured below are two examples of the defect...also pictured are two good ones.
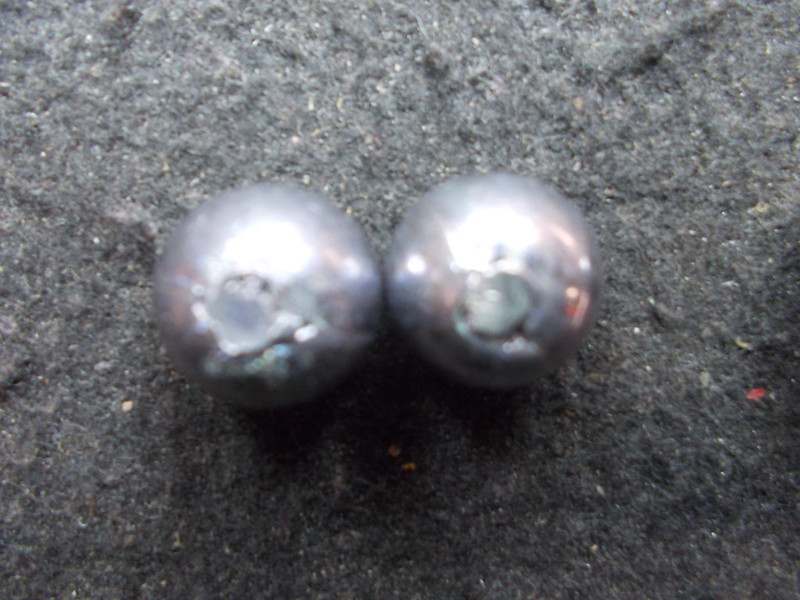
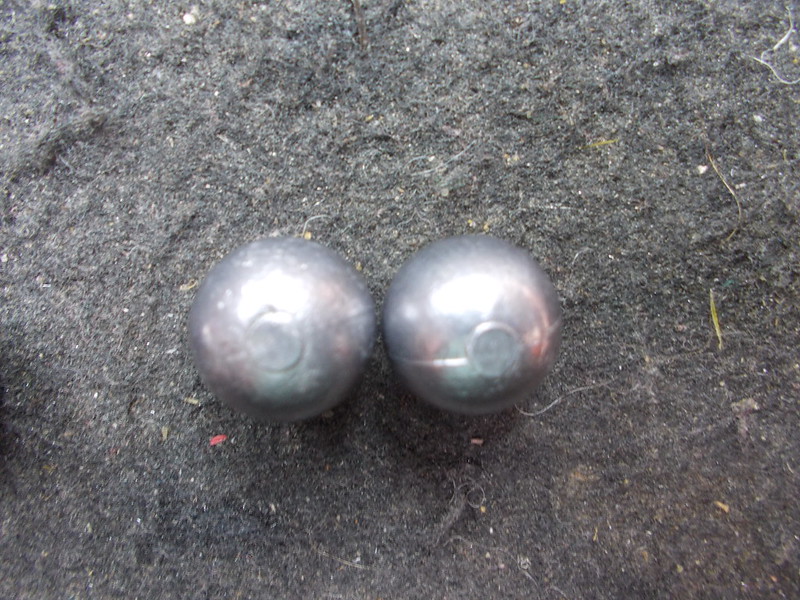
Since the weights and measurements were pretty good, I decided to do a 5-shot group with both types to see what happened. Pictures below are the results. Net, at 75 metres with the "good" balls a 2.25" group (measured center-to-center across the balls furthest apart. The "bad" balls had a 5.50 inch group. I swabbed the same between shots. There were no material delays in ignition or anything that would have caused me to flinch on any of these, so I think they are legitimate groups. Bench rested.
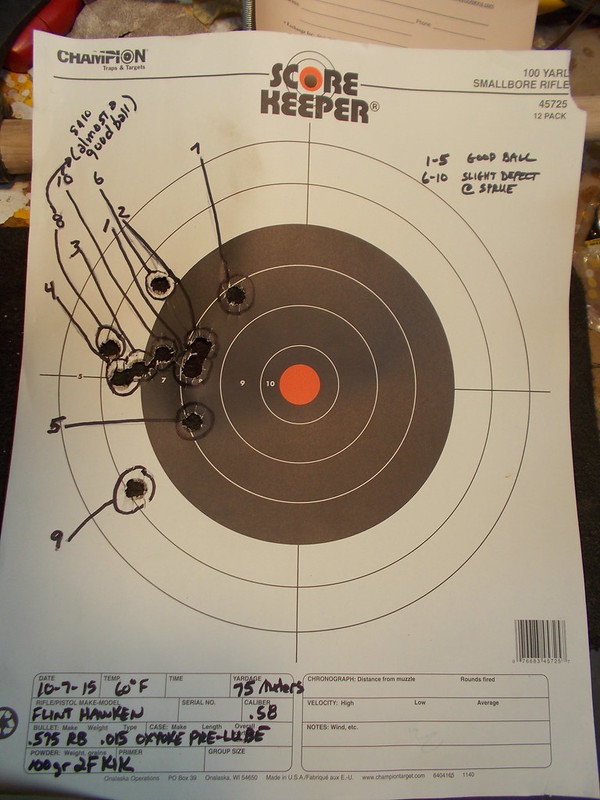
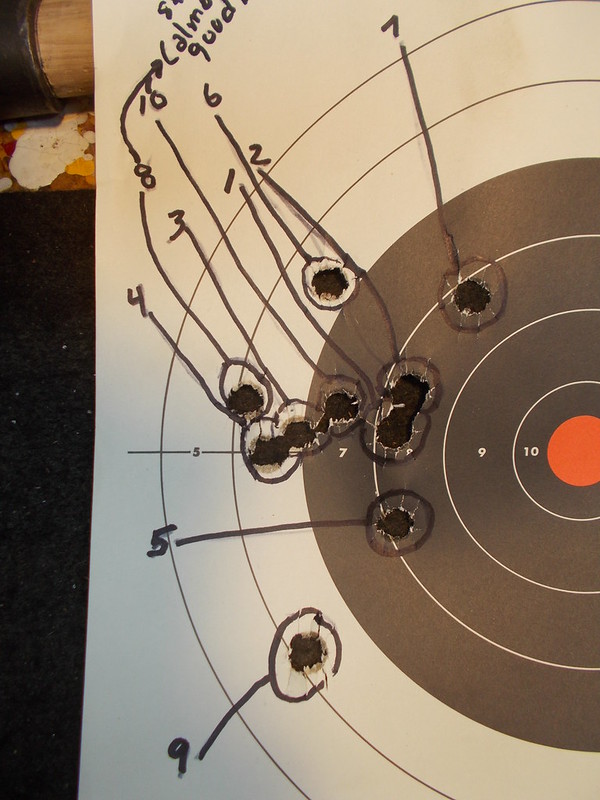
I really didn't think that this defect at the sprue would have this big of an impact, but clearly these ball need to go right back into the pot.
For those of you using Lee molds, have you experienced anything like this...the bridging issue, problems getting the cavity to fill properly unless you're running the lead very hot, etc.? I tried to keep the mold hot by holding it right on top of the pot while dipping, but clearly I was doing something wrong with this mold that I've not had any issue with while using my Lyman steel molds.
I also have to go back to some load development as the ToTW hand cast ball I used to work up my load turned out to be oversized by several thousandths...some even being bore sized! No wonder I was cutting patches, nearly bruising my hand on the short-starter, etc. Some poor quality control there. I'm going to bump my patch thickness a bit to "re-tighten" the load a bit and see if I can't get the "good ball" group shrunk down a bit. Need to tap that front sight over a bit too! :grin: