Mark Black
36 Cal.
- Joined
- Dec 28, 2011
- Messages
- 75
- Reaction score
- 1
I have a Dixie Gun Works southern mountain rifle. It's a poor boy, so it's not all dressed up or anything. I've been thinking about fitting/pouring a muzzle cap to protect the end grain. I know it's not pc for a poor boy, but i really want to protect the stock. Looking for some tips on pouring one. I've included some pics to give you an idea of shape and condition. Any help would be much appreciated!!
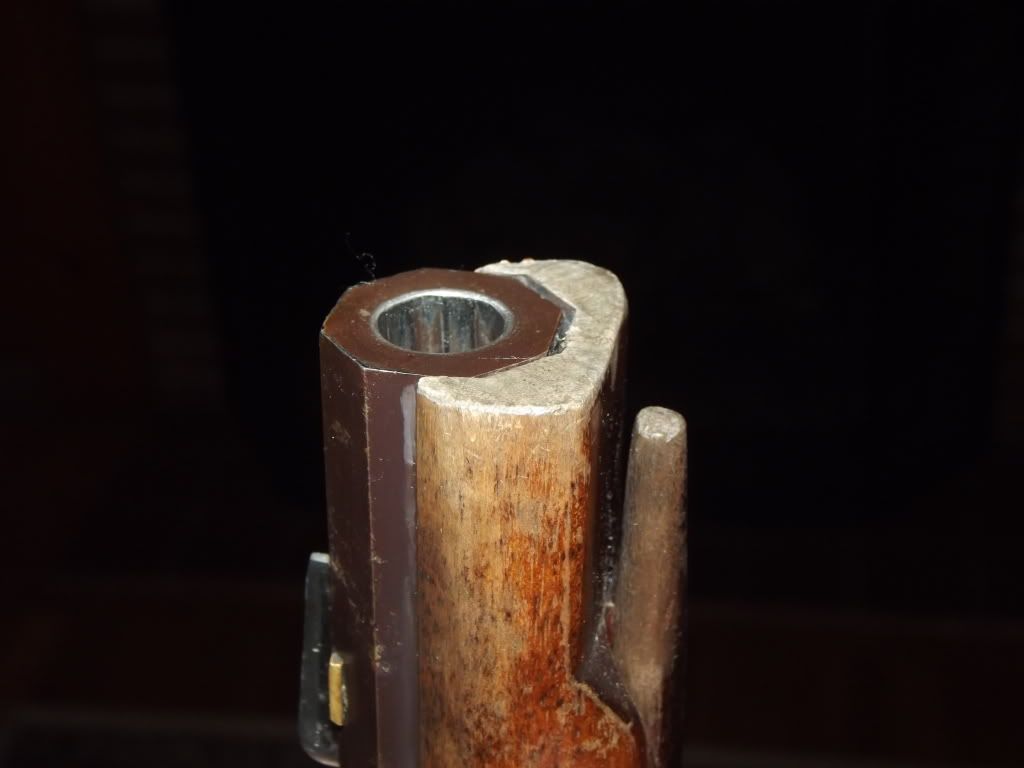
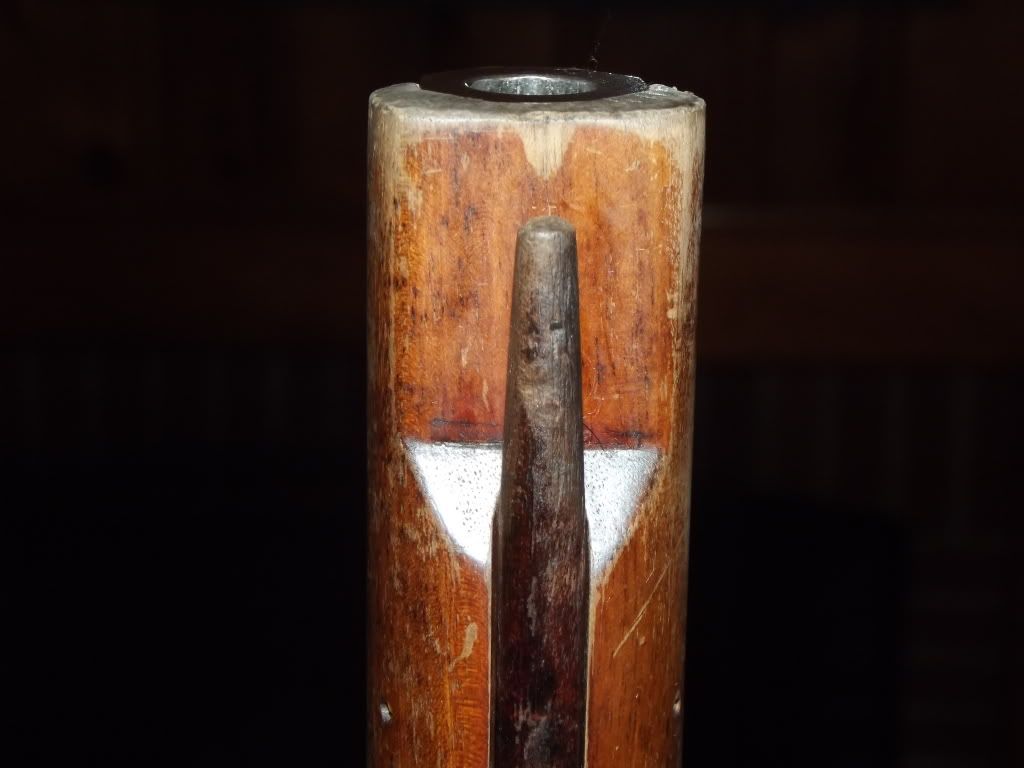
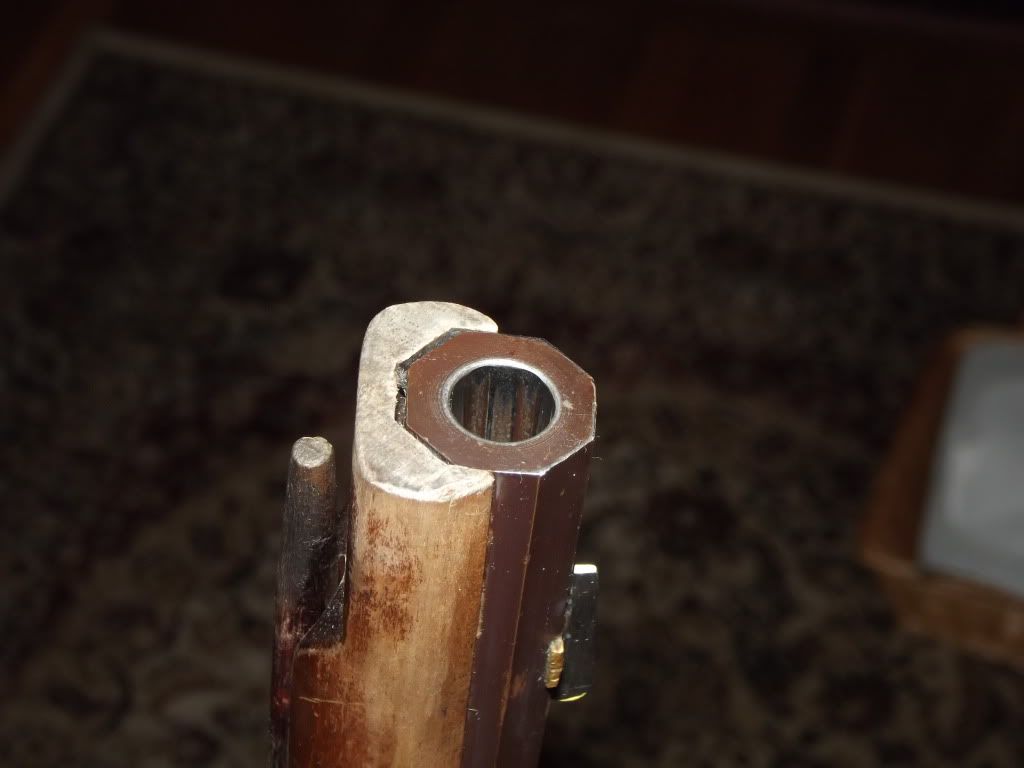