Erzulis boat
45 Cal.
- Joined
- Jul 14, 2005
- Messages
- 566
- Reaction score
- 78
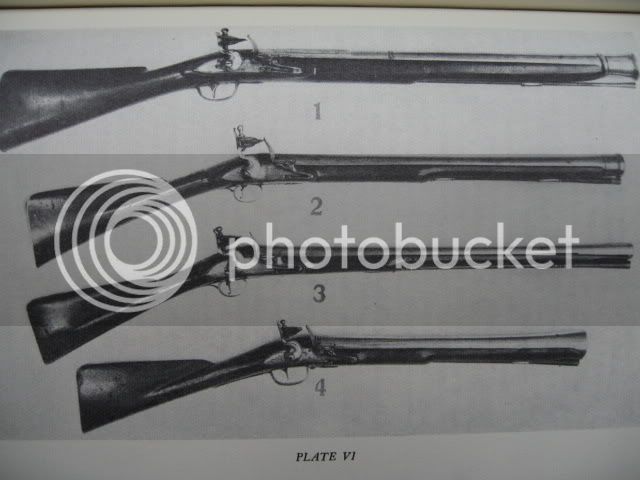
The build is the "Coaching Carbine" (Figure 3) and it has a 24" brass 17 bore barrel.
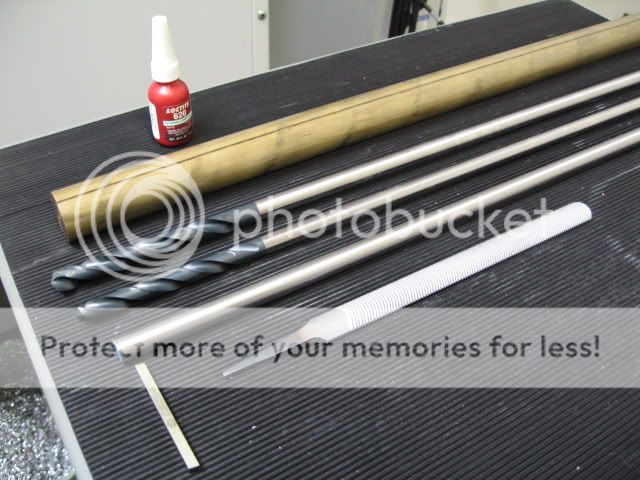
This is the material and basic tool layout.
The brass is a 27" long cylinder of alloy 485 with a yield strength of 54,000 PSI.
The drillbits are custom made from W01 drill rod and black oxide treated HSS. The bits are 7/16" and 1/2" in diameter. The fluted portion is a commercially available drillbit that was turned down at the shank to .300" by 1.15" long. The drill rod was bored to allow a press fit, and is retained by Loctite 620, and a .125 diameter pin.
The stock will be punched from both sides initially, then the 7/16" will go through followed by the 1/2".
The .649 (17 guage) bore will be made with a custom tool. You will note the 1/2" drill rod with the 3/16" square M2 cutter at a right angle to it. This cutter will be set into the end of the precision rod, and will become a cutter. I will post pictures of this configuration.
The bar with the cutter will be PULLED BACK through the 1/2" hole to create a perfect bore that is precisely piloted by the 1/2" precision shaft. Unlike a cannon barrel with a blind bore, a rifle/smoothbore barrel can be made very easily by the pull through method.
I will post the images on this procedure, and how to make the tool.