steved
40 Cal.
- Joined
- Feb 11, 2004
- Messages
- 253
- Reaction score
- 20
I more or less completed my work to restore a Walker percussion fowler that my buddy Flint62Smoothie passed along to me after he received it as a "frequent customer" gift from his local gun store. The main challenge I encountered in this effort was to find a replacement nipple because the cone was long gone on the original.
The threaded base measures .290" in diameter. I tried to replace it with a .285 x 28 AMPCO nipple from Muzzleloader Builders Supply (MBS) - the closest I could find after an extensive Internet search. It seemed to thread right in with a little wobble, so the threads appear to be 28 but the diameter is a little too small. The nipple is tight when fully seated but the wobble on the way in makes me think it would be too dangerous to shoot. Does anyone know where I can find a .290 x 28 nipple, or would I need to drill and tap the bolster for a 5/16 x 24 nipple?
The other challenge was to find a replacement hammer for the back action lock since the original hammer is cracked.
Can a cracked hammer be fixed by welding or forging? I don't have any welding experience or equipment so if it is possible to fix I would send it to a gunsmith to work on. I found out by trial and error that it is not so easy to find a suitable replacement hammer for a back action lock even if you find one with the right throw. I ordered two from Track but found that the geometry of the tumbler was not correct for the square opening in the TOW hammers. I finally located at MBS a back action hammer with no opening and I fitted the hammer to the tumbler. (The replacement had a butt-ugly dog head design that I tried to make less ugly by filing off the dog ears) The problem is, the replacement hammer is not nearly as thick as the original one, so the tumbler shaft stuck out high above the replacement hammer. I made a spacer/washer by cutting the head off a .30-06 cartridge and drilling out the primer hole until it fit over the tumbler shaft.
Any input on my questions about finding a replacement nipple and fixing a cracked hammer will be greatly appreciate.
BTW - here are a few before/after pictures of the restoration
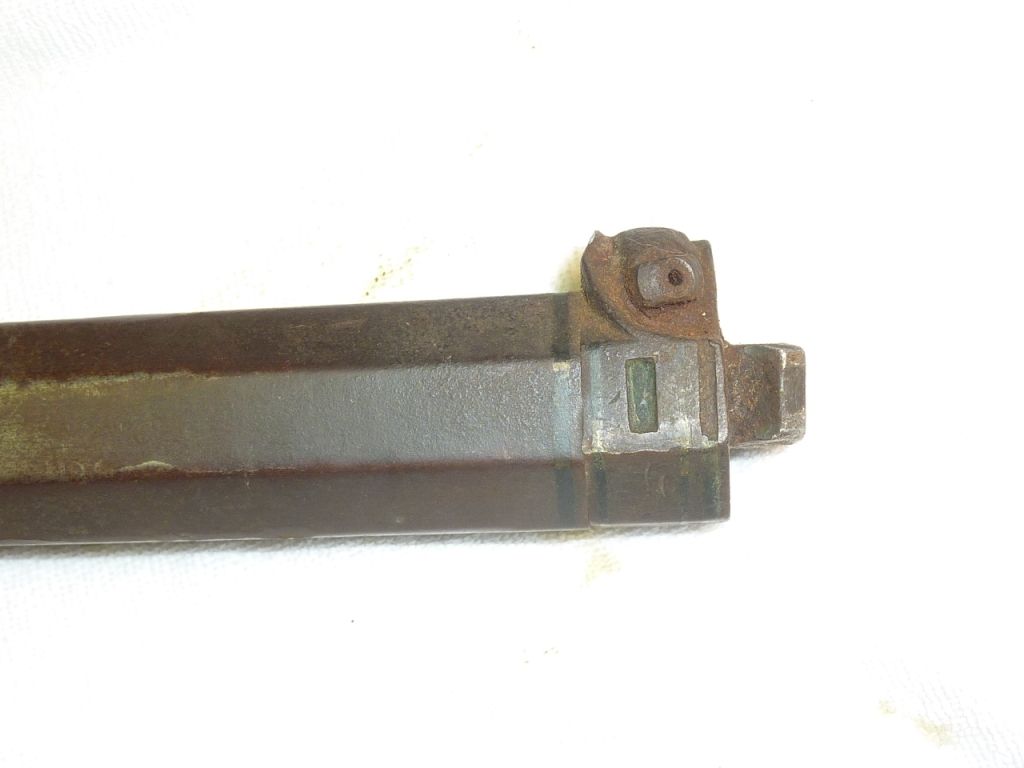
The threaded base measures .290" in diameter. I tried to replace it with a .285 x 28 AMPCO nipple from Muzzleloader Builders Supply (MBS) - the closest I could find after an extensive Internet search. It seemed to thread right in with a little wobble, so the threads appear to be 28 but the diameter is a little too small. The nipple is tight when fully seated but the wobble on the way in makes me think it would be too dangerous to shoot. Does anyone know where I can find a .290 x 28 nipple, or would I need to drill and tap the bolster for a 5/16 x 24 nipple?
The other challenge was to find a replacement hammer for the back action lock since the original hammer is cracked.
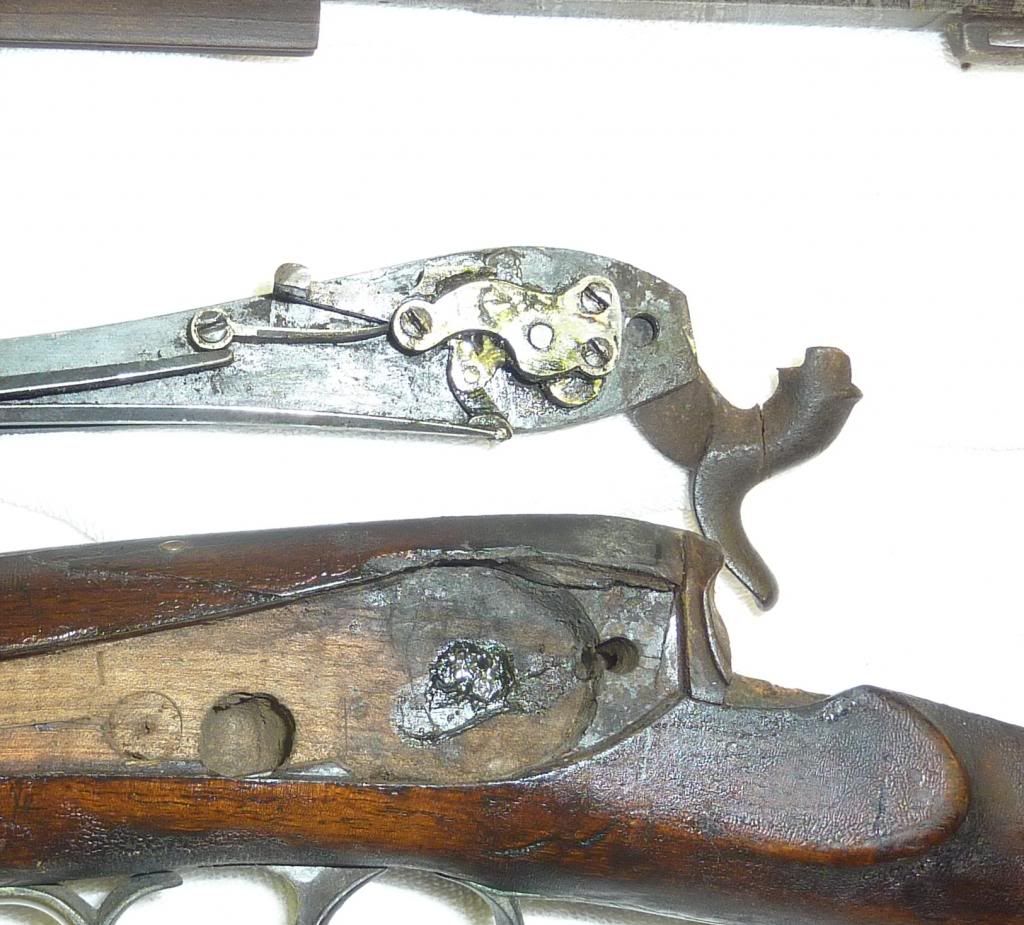
Can a cracked hammer be fixed by welding or forging? I don't have any welding experience or equipment so if it is possible to fix I would send it to a gunsmith to work on. I found out by trial and error that it is not so easy to find a suitable replacement hammer for a back action lock even if you find one with the right throw. I ordered two from Track but found that the geometry of the tumbler was not correct for the square opening in the TOW hammers. I finally located at MBS a back action hammer with no opening and I fitted the hammer to the tumbler. (The replacement had a butt-ugly dog head design that I tried to make less ugly by filing off the dog ears) The problem is, the replacement hammer is not nearly as thick as the original one, so the tumbler shaft stuck out high above the replacement hammer. I made a spacer/washer by cutting the head off a .30-06 cartridge and drilling out the primer hole until it fit over the tumbler shaft.
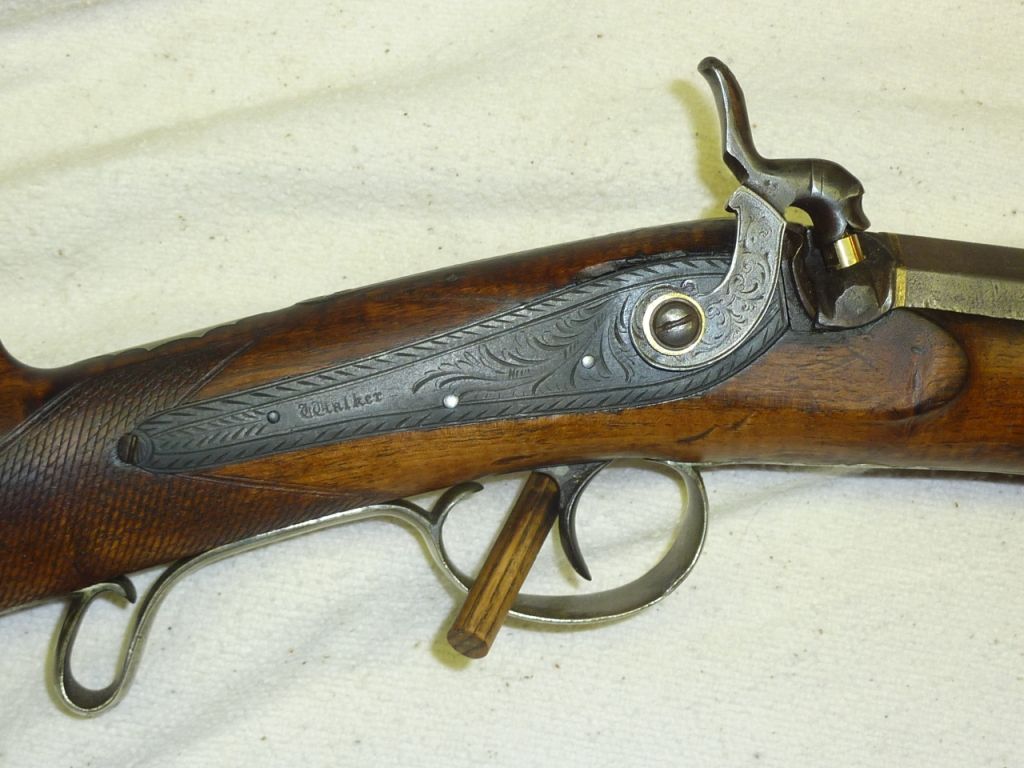
Any input on my questions about finding a replacement nipple and fixing a cracked hammer will be greatly appreciate.
BTW - here are a few before/after pictures of the restoration
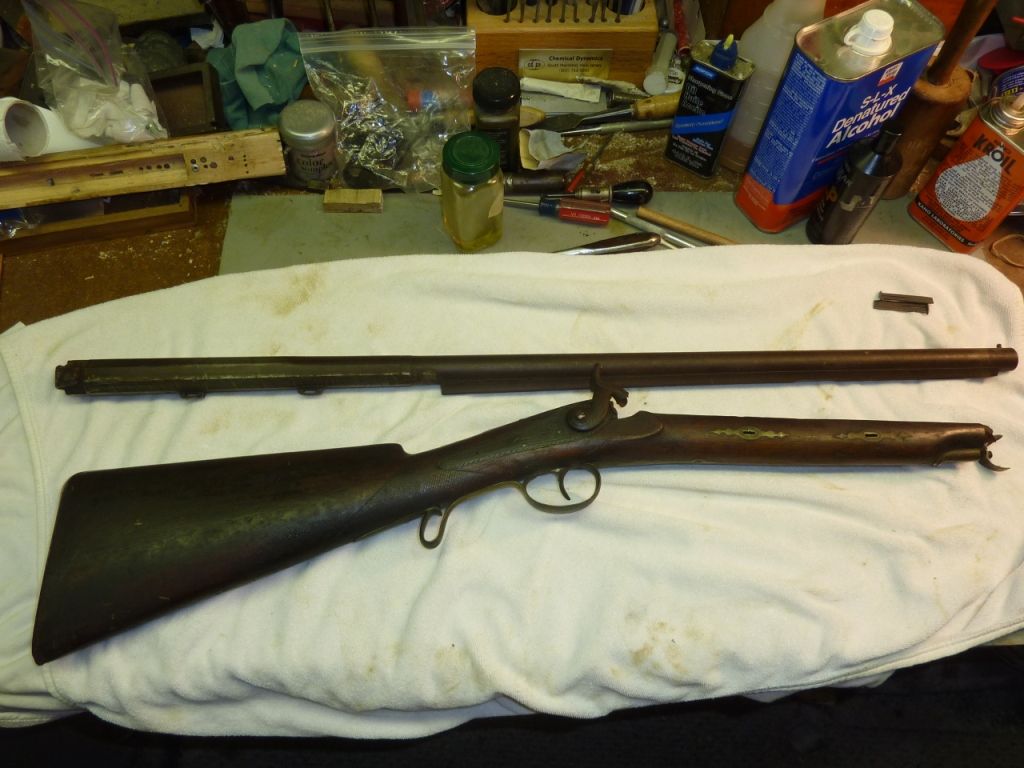
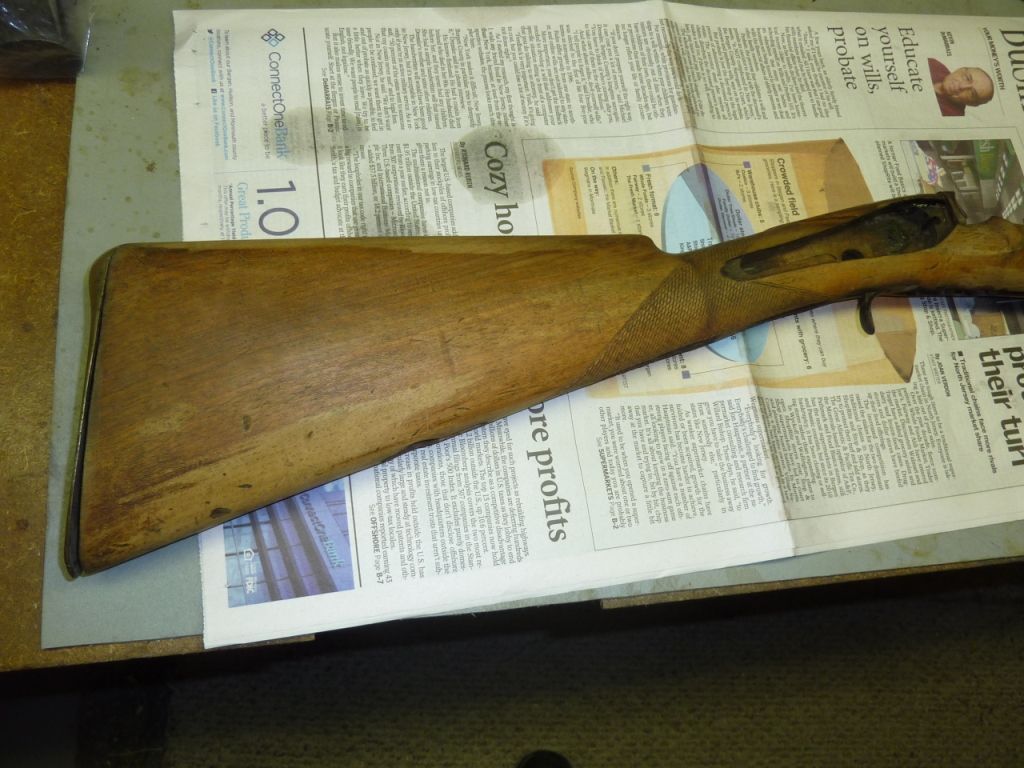
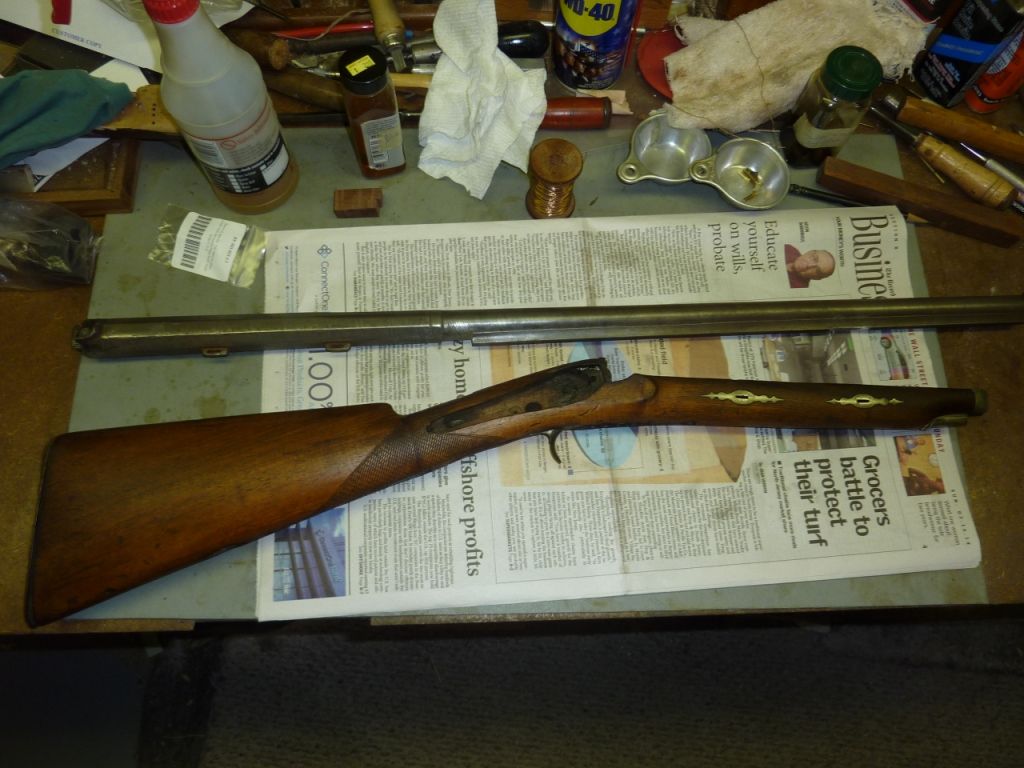

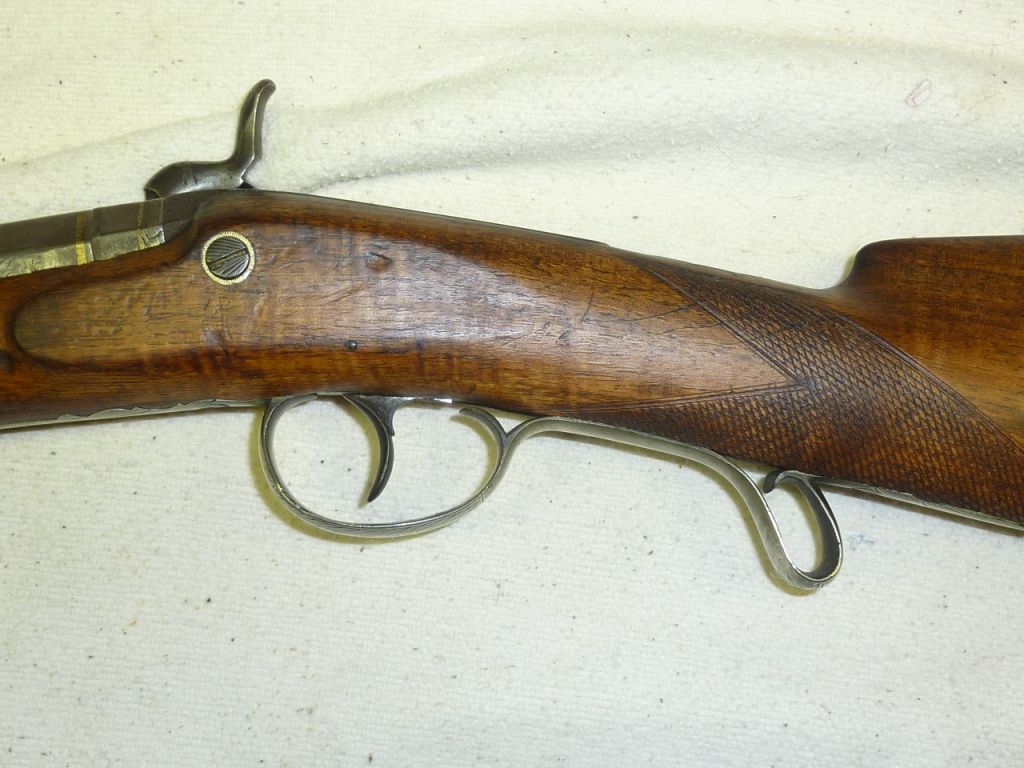