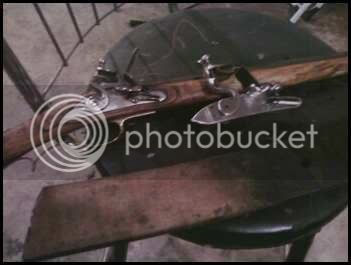
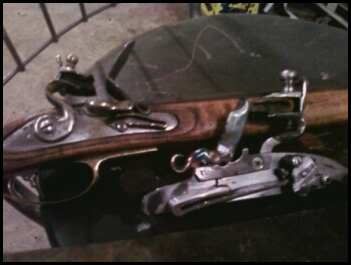
Having been recently called a fool and an idiot on this forum because I dont read the "how to" books, temper springs in an oven or use rake tines, exclusively, for forging springs, I feel compelled to share how I do it, anyway. These locks were hand made on a coal forge, entirely, from a piece of truck spring. (also shown in photo). Hardening and tempering were done at the forge with a bucket of water and a shovelfull of sand. The very small lock was used to build a child's rifle with a hand made .36 cal barrel and stocked in curled maple, cut from a tree found by an old farmhouse. The brass furniture was also hand made. The little rifle is only 41" overall length. The large lock is still being built. Pardon the phillips head screws. They are just temporary. Total cost for both: $0.00.
I'm not much of an artist and I don't call myself master of anything but I'm a pretty good mechanic. I've built dozens of rifles, pistols and muskets, and those for whom I've built have always been pleased. Incidently, I tried the suggested spider legs and chants but they don't seem to make any difference.