ApprenticeBuilder
58 Cal.
- Joined
- May 27, 2006
- Messages
- 2,528
- Reaction score
- 189
So,
I started working on this lock awhile back, this lock is for a Chambers Penn. Fowler in 20ga that our gun makers guild put together for a raffle.
This was my first go around using stones instead of sand paper of various grits backed with solid objects.
I started out with files to clean up 98% of the metal, I am not a fan of the perfect look on the rifles I build as it kind of takes away from the overall feel of the project.
I bought some stones in 320 and 600 grit and went to work on the lock plate, cock and top jaw. Once I had gone as far as I wanted with the 600 grit stones I engraved the lock plate and mounted it to a blocking plate and proceeded to color case harden it, the cock and top jaw, as this lock is only available from Chambers assembled there was no need to harden the internals.
I ended up needing to go thru the process of hardening the parts twice as I was just a bit to cool on the temp the first time and the parts did not get hard, second time thru it went perfect.
Once hard I tempered the parts back to relieve the brittleness, went back over them with the 600 grit stones again and hit it with OOOO steel wool and called it good.
Here are some pics for your perusal
Started the process
Here we are finished with the filework
I am pleased with the stones and the finish that they left, worth the investment for me.
Here is the lock plate mounted to the backing plate, kinda missed on my layout a bit but it still fits my crucible so no worries.
First quench, the blue is quite irridescent in the light, the parts were still soft at this point.
This is the second pass, I raised the temp of the parts at the time of quench another 50* and got the hardness I was looking for. Still got acceptable colors.
Finished assembled lock.
Open to critique, critisizm, opinions, etc.
I started working on this lock awhile back, this lock is for a Chambers Penn. Fowler in 20ga that our gun makers guild put together for a raffle.
This was my first go around using stones instead of sand paper of various grits backed with solid objects.
I started out with files to clean up 98% of the metal, I am not a fan of the perfect look on the rifles I build as it kind of takes away from the overall feel of the project.
I bought some stones in 320 and 600 grit and went to work on the lock plate, cock and top jaw. Once I had gone as far as I wanted with the 600 grit stones I engraved the lock plate and mounted it to a blocking plate and proceeded to color case harden it, the cock and top jaw, as this lock is only available from Chambers assembled there was no need to harden the internals.
I ended up needing to go thru the process of hardening the parts twice as I was just a bit to cool on the temp the first time and the parts did not get hard, second time thru it went perfect.
Once hard I tempered the parts back to relieve the brittleness, went back over them with the 600 grit stones again and hit it with OOOO steel wool and called it good.
Here are some pics for your perusal
Started the process
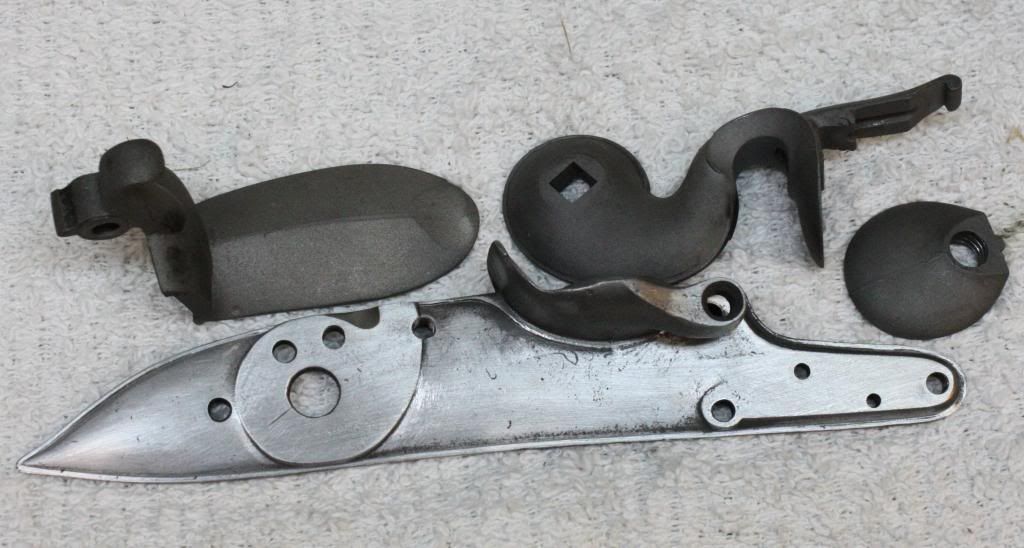
Here we are finished with the filework
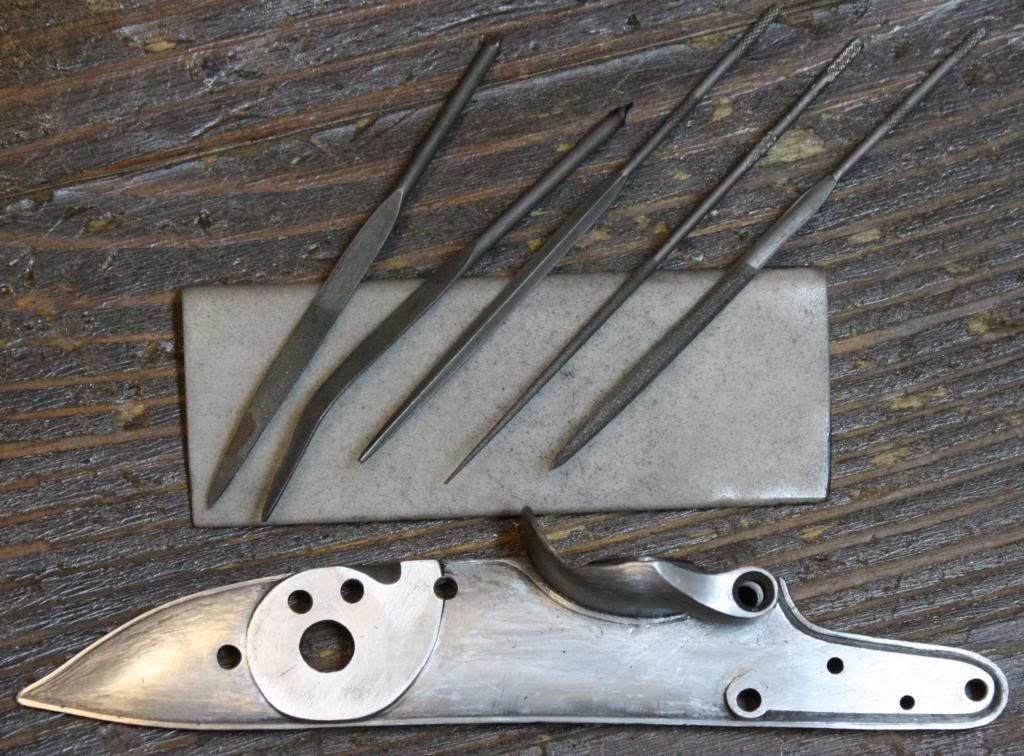
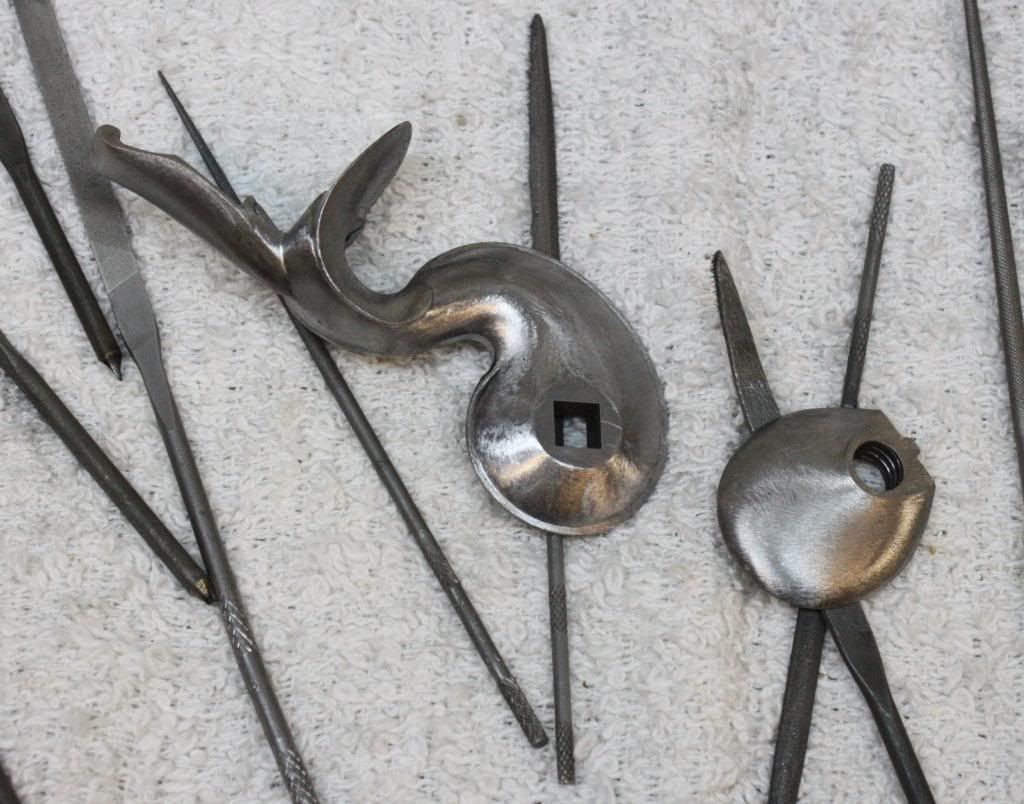
I am pleased with the stones and the finish that they left, worth the investment for me.
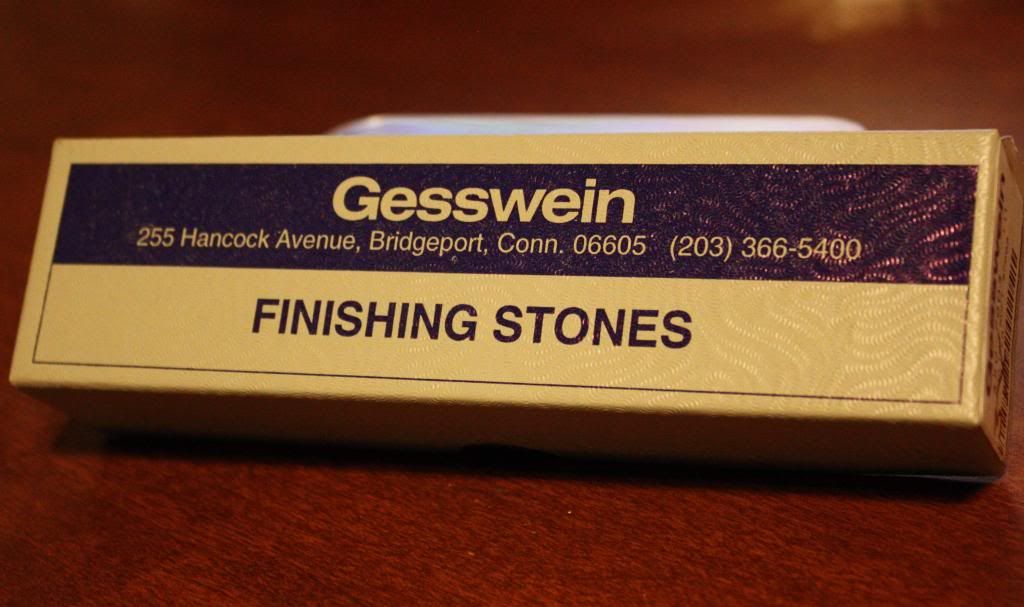
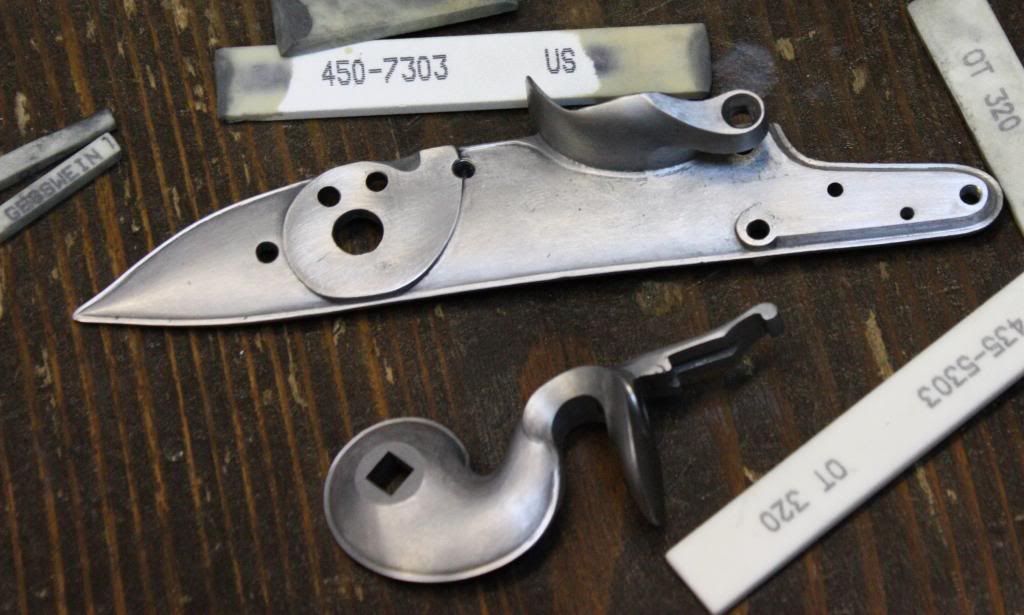
Here is the lock plate mounted to the backing plate, kinda missed on my layout a bit but it still fits my crucible so no worries.
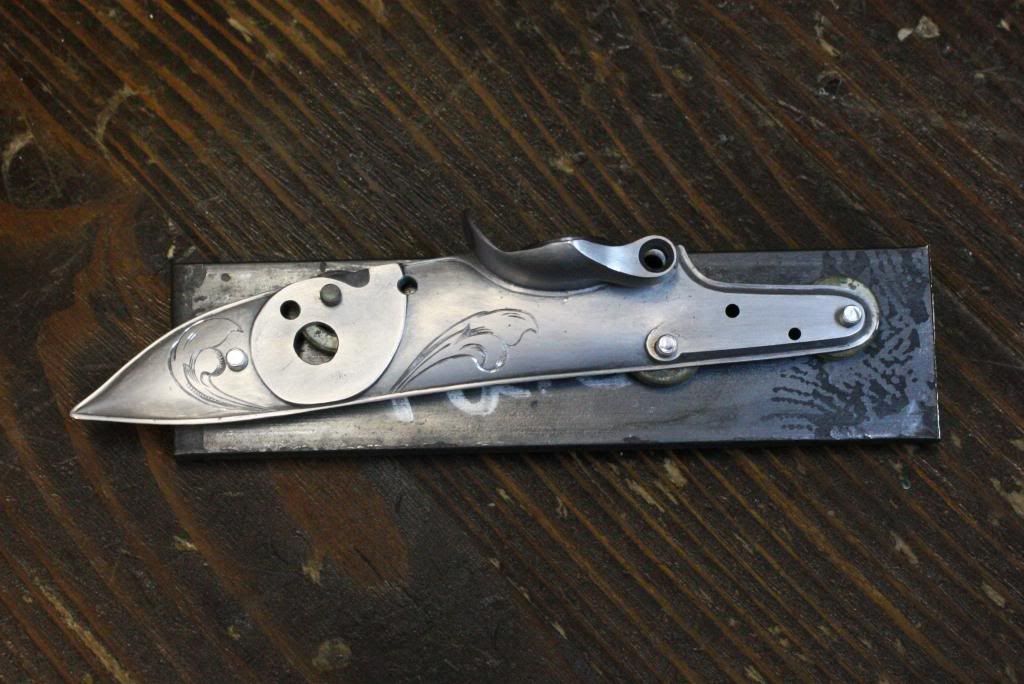
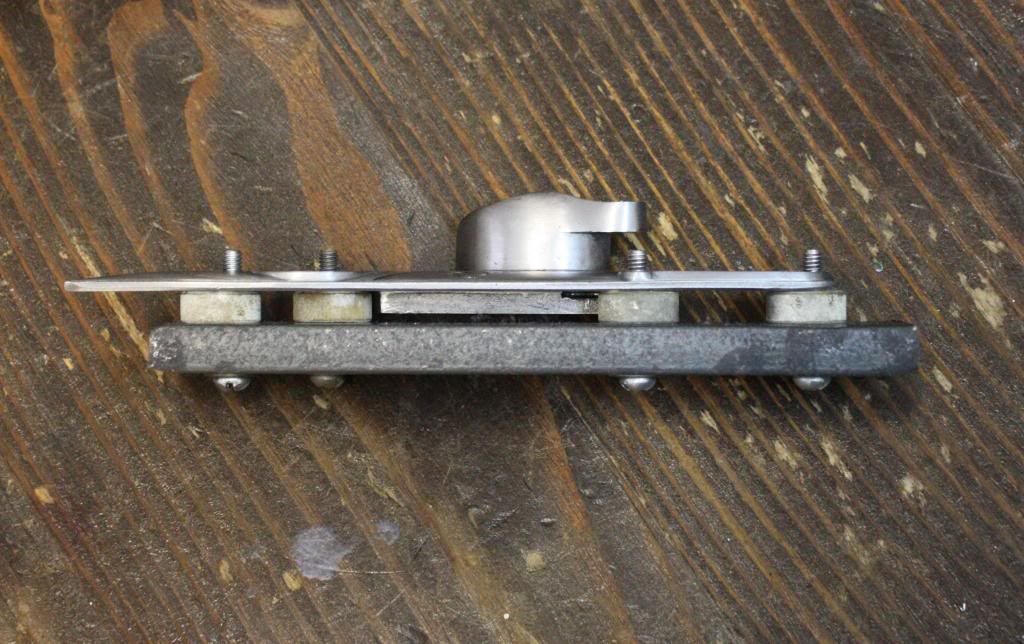
First quench, the blue is quite irridescent in the light, the parts were still soft at this point.
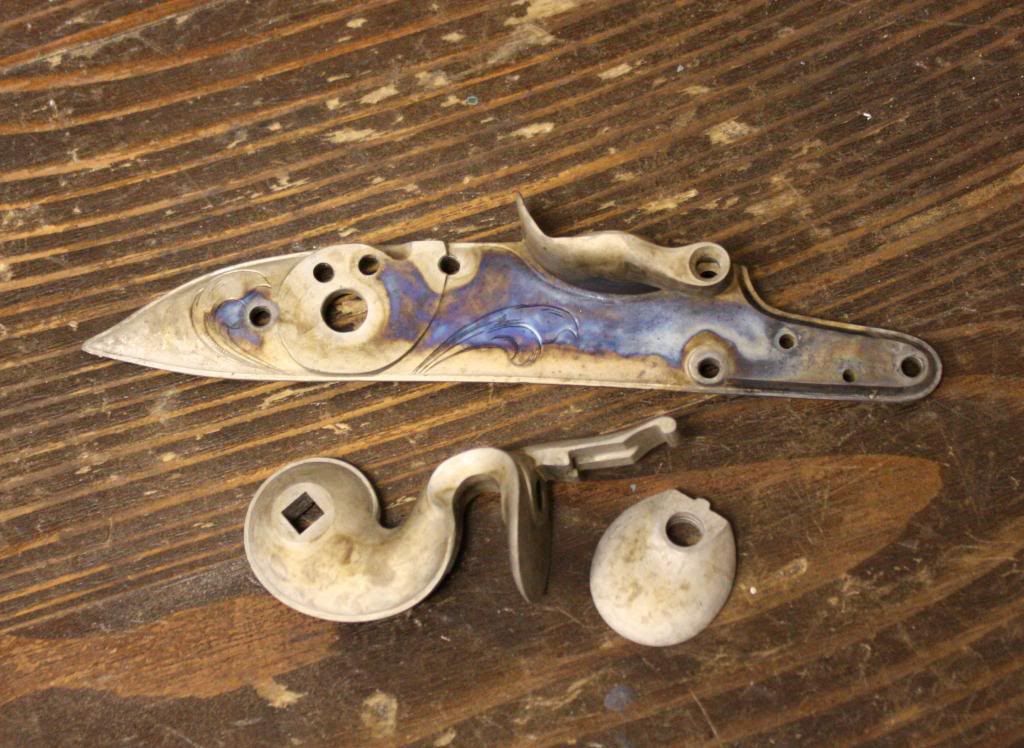
This is the second pass, I raised the temp of the parts at the time of quench another 50* and got the hardness I was looking for. Still got acceptable colors.
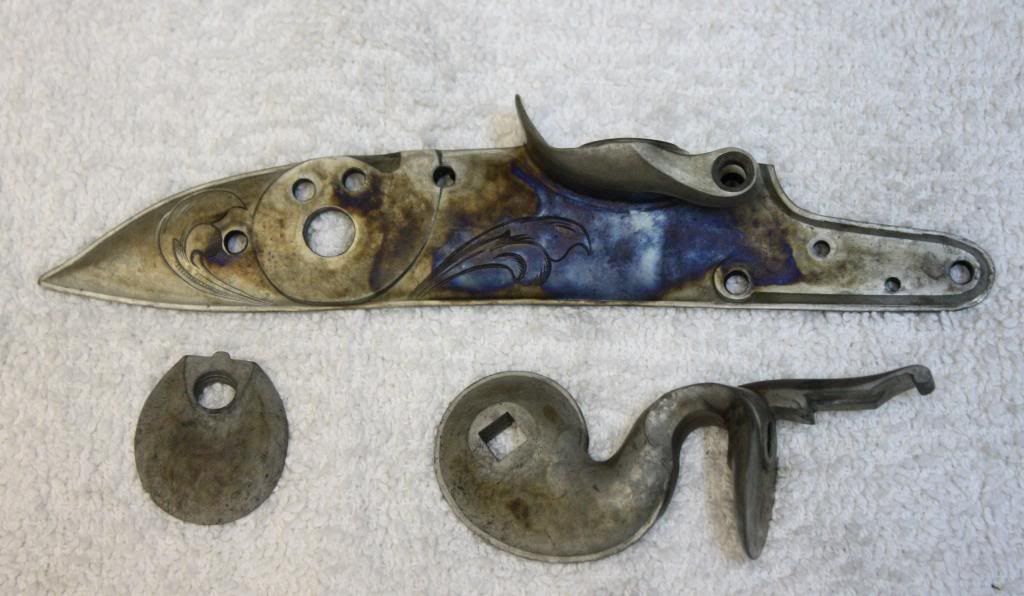
Finished assembled lock.
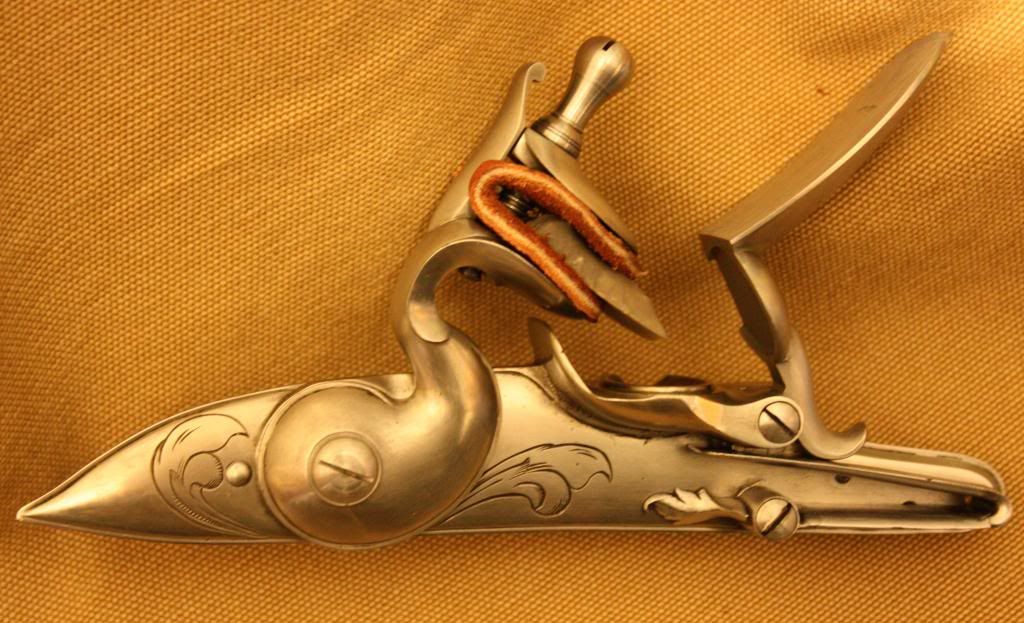
Open to critique, critisizm, opinions, etc.