- Joined
- Nov 26, 2005
- Messages
- 5,018
- Reaction score
- 9,972
Hi,
Holiday visiting and activities reduced my shop time. We finally got back to the Bess. Maria began inletting the butt plate while I began building the lock. The first step was cleaning up all the edges of the butt plate and flattening any that touched the wood as well as filing draft on the edges of the return. The casting was very good and clean but it also was hard for brass. It needed a lot of annealing to eliminate the springiness and resistance to filing. The machine inletting was off center, which we could mostly but not completely correct. It is minor and no one will notice in the end.
The first step is to locate and inlet the slot for the forward lug. This does not have to be precise and because the plate will move around a bit during inletting, making the slot a little oversized in all dimensions is a good thing to do, with the emphasis on a " little oversized". You have to inlet this plate straight down unlike later Bess pattern butt plates. So rask away most of the extra wood at the end of the stock allowing the butt face of the plate to rest close to the stock. That stock and face of the plate should be almost straight. Then bend the front of the tang from the under lug forward up so it allows the tang behind it to be partially inlet without the front interfering. Set the buttplate down into the stock and trace the rear 2/3s of the tang on the wood. Stab in that outline and remove the interior wood until the plate sets down into the mortice. Now check how the face plate meets the stock and the rear of the tang. When they are well fitted, bend the forward part of the tang down level with the rest of the butt plate, trace it on the wood, and inlet the mortise. Here is our end result and I doubt you can find a better job.
However, I make that brag with one huge caveat. The black walnut used on this stock is very difficult to work. It chips, collapses, and shreds with minor pressure. It is almost impossible to do detailed inletting. Consequently, I added stained AcraGlas along all the edges of the tang. The inletting we did was precise but shredded and cracking wood bordered much of the mortise ready to be torn out. So I smeared AcraGlas on the edges of the mortice and over the cracks in the stock along the edges of the mortise. The butt plate fit tight and pressed most of the epoxy out but also into the wood along the edges. That solved the problem and strengthened the entire mortise, but most importantly, the wood adjacent to the butt plate. I am afraid we will have to do the same for the trigger guard.
We started building the lock. I trued up the tumbler on my lathe so the round post for the flint cock and post for the bridle were perfectly concentric and true. I also trued up the sides of the tumbler. Once that is done, I accurately measure the diameter of the tumbler post and drill a slightly undersized hole for it through the lock plate. I use the TRS witness mark to center that hole. Then I file or stone the hole until the tumbler begins to fit tightly. I fit the flint cock on the tumbler and then use it to rotate the tumble in the lock plate to lap it into place. I smear valve grinding compound and paraffin oil on the tumbler post and then place it in the plate, attach the flint cock, and rotate it back and forth until it fits precisely and smoothly in the lock plate.
While working on the Bess, Maria is also working on building a very fine Joseph Griffin English lock from castings by Blackley in the UK.
We have a very busy shop.
dave
Holiday visiting and activities reduced my shop time. We finally got back to the Bess. Maria began inletting the butt plate while I began building the lock. The first step was cleaning up all the edges of the butt plate and flattening any that touched the wood as well as filing draft on the edges of the return. The casting was very good and clean but it also was hard for brass. It needed a lot of annealing to eliminate the springiness and resistance to filing. The machine inletting was off center, which we could mostly but not completely correct. It is minor and no one will notice in the end.
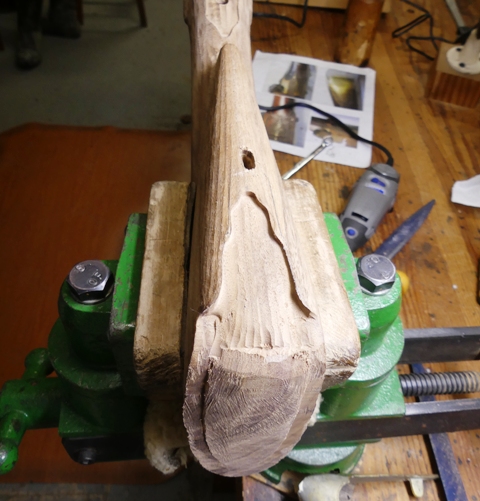
The first step is to locate and inlet the slot for the forward lug. This does not have to be precise and because the plate will move around a bit during inletting, making the slot a little oversized in all dimensions is a good thing to do, with the emphasis on a " little oversized". You have to inlet this plate straight down unlike later Bess pattern butt plates. So rask away most of the extra wood at the end of the stock allowing the butt face of the plate to rest close to the stock. That stock and face of the plate should be almost straight. Then bend the front of the tang from the under lug forward up so it allows the tang behind it to be partially inlet without the front interfering. Set the buttplate down into the stock and trace the rear 2/3s of the tang on the wood. Stab in that outline and remove the interior wood until the plate sets down into the mortice. Now check how the face plate meets the stock and the rear of the tang. When they are well fitted, bend the forward part of the tang down level with the rest of the butt plate, trace it on the wood, and inlet the mortise. Here is our end result and I doubt you can find a better job.
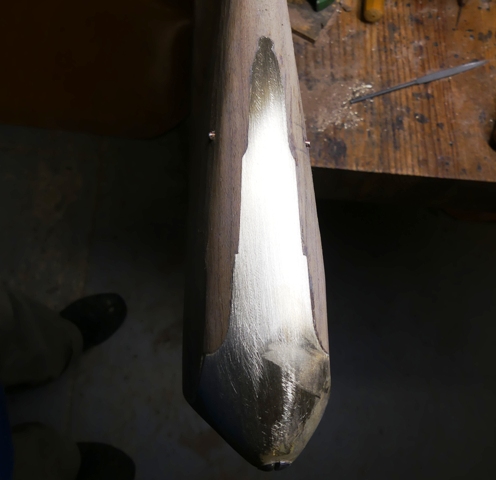
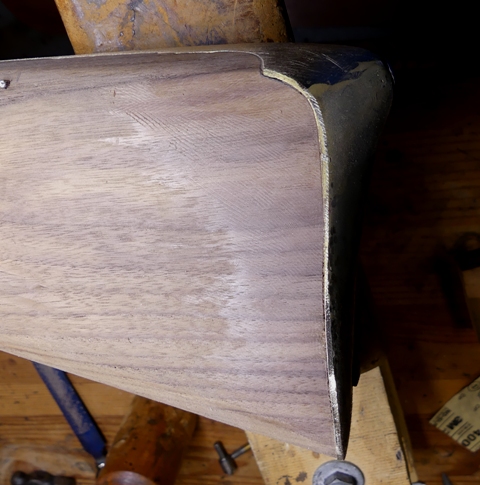
However, I make that brag with one huge caveat. The black walnut used on this stock is very difficult to work. It chips, collapses, and shreds with minor pressure. It is almost impossible to do detailed inletting. Consequently, I added stained AcraGlas along all the edges of the tang. The inletting we did was precise but shredded and cracking wood bordered much of the mortise ready to be torn out. So I smeared AcraGlas on the edges of the mortice and over the cracks in the stock along the edges of the mortise. The butt plate fit tight and pressed most of the epoxy out but also into the wood along the edges. That solved the problem and strengthened the entire mortise, but most importantly, the wood adjacent to the butt plate. I am afraid we will have to do the same for the trigger guard.
We started building the lock. I trued up the tumbler on my lathe so the round post for the flint cock and post for the bridle were perfectly concentric and true. I also trued up the sides of the tumbler. Once that is done, I accurately measure the diameter of the tumbler post and drill a slightly undersized hole for it through the lock plate. I use the TRS witness mark to center that hole. Then I file or stone the hole until the tumbler begins to fit tightly. I fit the flint cock on the tumbler and then use it to rotate the tumble in the lock plate to lap it into place. I smear valve grinding compound and paraffin oil on the tumbler post and then place it in the plate, attach the flint cock, and rotate it back and forth until it fits precisely and smoothly in the lock plate.
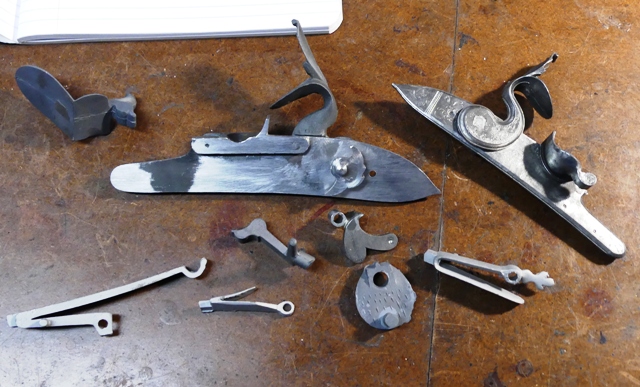
While working on the Bess, Maria is also working on building a very fine Joseph Griffin English lock from castings by Blackley in the UK.
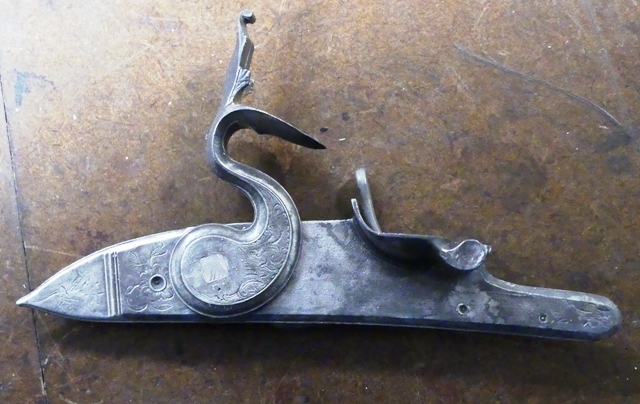
We have a very busy shop.
dave