My son bought me the parts for building a Bowie knife from Crazy Crow Trading Post for Christmas and I have some questions.
To let you know what I have, the blade is the 6" Bowie they offer. The tang is .160" thick X 1/2" X 4" with one 3/16" hole thru it.
He bought 5 rivet sets? There are two brass rivets in each bag. One is solid, one has a hole in it but it seems to be too small for the solid one to slip into it without pounding.
The body of the hollow one is .150" diameter X .62 long. The solid one's body is .120 diameter X .62" long. The heads are .305 diameter X .04 thick.
For a handle, I got a block of curly maple that measures 2" X 2" X 6".
The guard is a flat oval shaped piece 3/16" thick X .71" wide X 2.25 long.
The Butt is a shaped, round piece 1.09" in diameter at the large end, .870" at the small end. It has a .510" X .390" deep hole in the small end that does fit over the tang and what appears to be a .400" diameter hole for a screw in the large end.
It looks like this
I think my first question is, should I cut the wood in half and carve out a pocket in each piece to clear the tang?
I don't think drilling a 1/2" hole in the block to clear the tang and then filling it with epoxy would be a good way to go.
To let you know what I have, the blade is the 6" Bowie they offer. The tang is .160" thick X 1/2" X 4" with one 3/16" hole thru it.
He bought 5 rivet sets? There are two brass rivets in each bag. One is solid, one has a hole in it but it seems to be too small for the solid one to slip into it without pounding.
The body of the hollow one is .150" diameter X .62 long. The solid one's body is .120 diameter X .62" long. The heads are .305 diameter X .04 thick.
For a handle, I got a block of curly maple that measures 2" X 2" X 6".
The guard is a flat oval shaped piece 3/16" thick X .71" wide X 2.25 long.
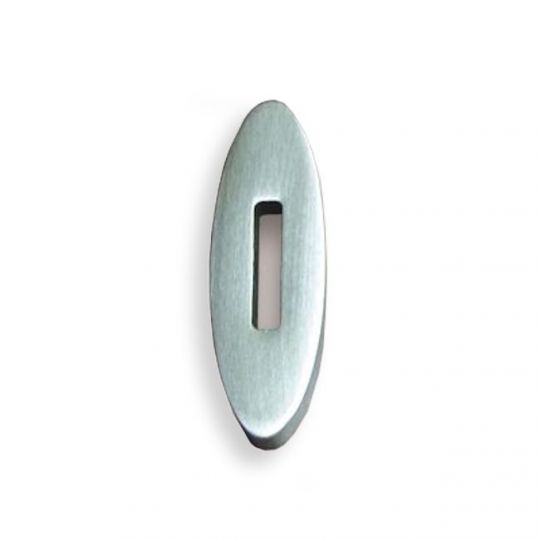
The Butt is a shaped, round piece 1.09" in diameter at the large end, .870" at the small end. It has a .510" X .390" deep hole in the small end that does fit over the tang and what appears to be a .400" diameter hole for a screw in the large end.
It looks like this

I think my first question is, should I cut the wood in half and carve out a pocket in each piece to clear the tang?
I don't think drilling a 1/2" hole in the block to clear the tang and then filling it with epoxy would be a good way to go.